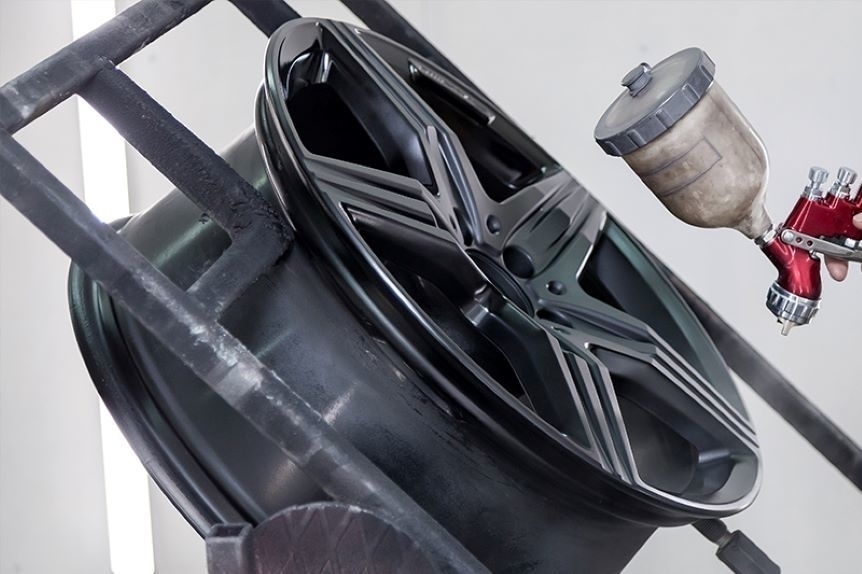
Ver traducción automática
Esta es una traducción automática. Para ver el texto original en inglés haga clic aquí
#Novedades de la industria
Producción de llantas de aleación: la importancia de la pintura
Control de la temperatura
En el fascinante mundo de la industria del automóvil, donde el rendimiento se une a la elegancia, la producción de llantas de aleación es un capítulo crucial. Este sofisticado proceso, que combina ingeniería y diseño, requiere una atención meticulosa en cada etapa. En las siguientes secciones, exploraremos las facetas de este proceso, desde la elección de los materiales hasta el acabado y la pintura, que confieren durabilidad y belleza a estos importantes accesorios del automóvil.
Selección de materiales
Las llantas de aleación, una vez instaladas, estarán sometidas a grandes esfuerzos. Por consiguiente, la elección de los materiales adecuados para su construcción es el paso clave para garantizar la calidad del rendimiento del producto final.
Una llanta de aleación, como su nombre indica, está compuesta por una aleación de varios metales. La elección y proporción de estos materiales se basa en la experiencia acumulada a lo largo del tiempo por la empresa fabricante, y puede cambiar con el tiempo en función de las necesidades del mercado y de las últimas innovaciones tecnológicas.
De todos los metales, el aluminio es el más utilizado en la mayoría de llantas de aleación del mercado actual. Su popularidad se debe a su ligereza y facilidad de procesamiento. Este elemento nunca se utiliza puro, sino mezclado con otros metales para mejorar sus propiedades mecánicas.
Para las llantas de aleación de gama alta o de competición, se suelen utilizar aleaciones de magnesio. El uso de este metal permite obtener llantas igual de resistentes a los choques y las vibraciones, pero hasta un 35% más ligeras que sus homólogas de aluminio.
Fusión
Una vez seleccionados los materiales, pasamos al proceso de fundición, cuyo objetivo es crear la aleación metálica con la que se fabricarán las llantas.
La fusión tiene lugar en un horno de fusión especial, a temperaturas de hasta 1.000 grados centígrados. Los fabricantes siguen esta etapa con mucha atención, controlando cuidadosamente la composición de la aleación mediante análisis espectrales de emisión óptica. Este control permite conocer las cantidades exactas de diversos elementos fundidos dentro de la aleación.
Si todo es conforme a la norma, la aleación metálica se vierte en el molde de la llanta. Aquí, el material se enfría y se prensa para llenar completamente el molde.
Forja
La forja es un proceso alternativo a la fundición que adoptan los fabricantes que pretenden ofrecer productos de gama alta. Garantiza una distribución uniforme de las características físicas de la llanta, evitando las inhomogeneidades entre las distintas zonas. Una llanta forjada presenta mejoras significativas en términos de respuesta a tensiones e impactos y, en consecuencia, también muestra un menor riesgo de deformación. Otra ventaja es una mayor resistencia para el mismo material utilizado. Estas características permiten que las llantas forjadas sean delgadas y ligeras.
Los costes de forja son más elevados que los de fundición. Esto se debe tanto a que es un proceso laborioso como al elevado desperdicio de material durante la producción.
El proceso de forja comienza con la fusión del material, que se somete a una presión muy alta dentro de un disco redondo. Posteriormente, el disco se moldea en forma de llanta mediante una serie de compresiones y calentamientos hasta alcanzar la forma prevista por el modelo específico.
Acabado
La fase de acabado es esencial para garantizar no sólo la funcionalidad, sino también la estética de la llanta de aleación. Esta etapa incluye varios tratamientos, entre ellos:
la rectificación, es decir, la corrección de posibles asimetrías o imperfecciones
la eliminación de manchas
La creación del agujero central
El anodizado, que hace que la llanta sea más resistente a la corrosión y mejora su impacto estético
Estas operaciones no son fáciles de automatizar, sino que requieren la experiencia y los conocimientos de trabajadores cualificados.
Tras el acabado, se elimina el polvo para garantizar la uniformidad y limpieza de la superficie de la llanta.
El proceso de producción continúa con la última etapa.
Pintura
La pintura de llantas de aleación, contrariamente a lo que se pueda creer, es una actividad compleja y delicada. Para conseguir un resultado excelente, es esencial mantener bajo control todas las fases del proceso.
La técnica más utilizada es la pintura en polvo. El método consiste en aplicar un fino polvo coloreado a la superficie de las llantas, seguido de un calentamiento en un horno de pintura. Con la exposición al calor, el polvo se licua, cubriendo uniformemente la llanta.
Un aspecto clave del proceso de recubrimiento es la correcta manipulación de las altas temperaturas. La supervisión y el control precisos son cruciales para garantizar un revestimiento duradero y homogéneo. Las temperaturas inferiores a las óptimas pueden causar defectos y desigualdades en el revestimiento, comprometiendo tanto la estética como la funcionalidad de la llanta.
En este contexto, Tecnosoft ha introducido una solución innovadora para garantizar un control adecuado de las altas temperaturas durante el pintado.
Como muchos de nuestros productos, todo empezó con una petición muy concreta de un cliente.
Control de la temperatura durante el pintado de llantas de aleación
Una conocida empresa de fabricación de llantas para automóviles se enfrentaba a un exigente reto. Su objetivo era supervisar un proceso de pintado para garantizar que cada llanta fuera no solo estéticamente impecable, sino también excepcionalmente duradera.
La pintura en hornos industriales requiere temperaturas y tiempos muy precisos, por lo que es necesaria una supervisión constante.
Este es el ciclo de temperatura adoptado por la empresa para pintar sus llantas de aleación:
La primera fase tiene lugar en un primer horno calentado a 250°C, donde los círculos permanecen durante 15 minutos.
A continuación tiene lugar la fase intermedia, una pausa en la que se baja la temperatura a 25°C durante 30 minutos.
El círculo pasa al segundo horno calentado a 250°C. Esta vez durante un periodo más largo, 45 minutos.
Un segundo intermedio de 40 minutos a 100°C seguido de un tercer intermedio de 30 minutos a 25-30°C.
A continuación, el borde pasa a un tercer horno a 250°C durante 35 minutos.
Por último, se pasa a la fase de enfriamiento.
Por tanto, para controlar la temperatura era necesario encontrar instrumentos de medición capaces de soportar temperaturas muy elevadas durante periodos de tiempo relativamente largos. Un reto tecnológico que abordamos paso a paso.
Fase 1: Estudio preliminar
Nuestro objetivo era crear un sistema de monitorización que pudiera soportar el calor y proporcionar datos precisos sobre la temperatura en varios puntos de la llanta durante el pintado.
Por lo tanto, el estudio de viabilidad se centró en verificar el rendimiento del sistema de termopares TC-Log 8 S USB bajo las altas temperaturas típicas de los hornos de pintura.
En esta fase, comprobamos la protección térmica disponible para los termopares, pero descubrimos que no eran adecuados para todo el proceso de pintura, ya que sólo podían soportar hasta la mitad del proceso de calentamiento.
Por tanto, fue necesario encontrar una solución a medida adecuada para este fin.
Paso 2: Creación de soluciones
Para superar la limitación, modificamos la carcasa metálica exterior de la protección térmica existente, sustituyendo el material interior por un compuesto más resistente.
Además, para evitar la dispersión de polvo que pudiera interferir con la pintura, cubrimos el nuevo material con un revestimiento adecuado.
Para aumentar el aislamiento térmico y retrasar al máximo la penetración del calor, también hemos añadido dos pequeños depósitos metálicos que contienen agua con una válvula de ventilación.
¡Nuestro prototipo había salido así a la luz!
Fase 3: La prueba final
Una vez disponible el prototipo, lo sometimos al mismo ciclo térmico solicitado por el cliente.
El resultado fue muy positivo: de hecho, la prueba térmica se superó brillantemente. El instrumento fue capaz de controlar temperaturas de 250° durante un tiempo prolongado manteniendo un margen de seguridad ampliamente satisfactorio.
Retos superados:
En el desarrollo de nuestro sistema de termopares para monitorizar temperaturas en procesos de pintura, superamos dos retos:
El primero y más desafiante fue el rediseño completo de la protección térmica. No se trataba de una simple revisión, sino de crear una solución completamente nueva que tuviera en cuenta los requisitos específicos del proceso de pintura a alta temperatura.
Paralelamente, rediseñamos la carcasa del sistema electrónico. Este paso era crucial para garantizar que el sistema no sólo resistiera las altas temperaturas, sino que también siguiera siendo funcional y fiable en estas condiciones extremas. Así pues, probamos con éxito un nuevo aislamiento para ofrecer una protección térmica superior sin comprometer la funcionalidad del sistema.
El próximo reto
Para un futuro próximo estamos estudiando una caja externa que pueda contener la protección térmica del registrador de datos.
El objetivo es que el sistema pueda utilizarse en el 100% de los proyectos de los clientes, una meta ambiciosa que requerirá más innovación y experimentación.
Estos retos superados y futuros demuestran nuestro compromiso permanente de ofrecer soluciones a medida que satisfagan con eficacia y precisión las necesidades específicas de nuestros clientes.
Llevamos 35 años ampliando nuestros conocimientos y consolidando nuestra posición de liderazgo en el campo de la supervisión de procesos industriales complejos.
Póngase en contacto con nosotros