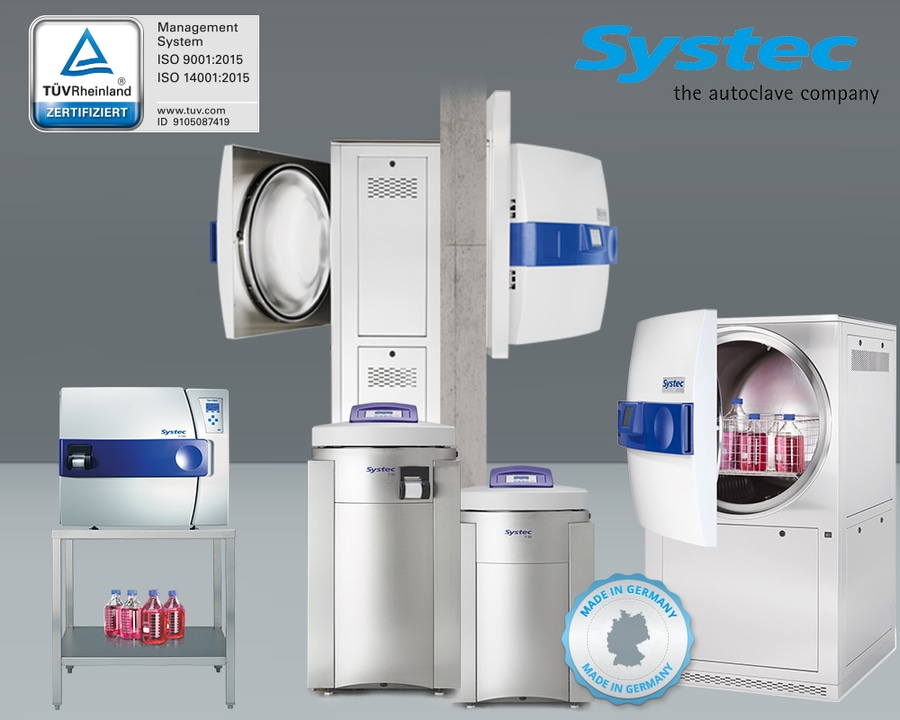
Ver traducción automática
Esta es una traducción automática. Para ver el texto original en inglés haga clic aquí
#Tendencias de productos
Calificación y validación de las autoclaves del laboratorio
Validación de autoclaves
La necesidad de calificar una autoclave y de validar el proceso de la esterilización se presenta de diversas leyes y regulaciones. Aunque la calificación y la validación de los términos se mencionen en la frase de Qualification_Validationone o aún se utilicen generalmente sinónimo, las diversos declaraciones y acercamientos se ocultan detrás de ellas.
La necesidad para calificar una autoclave y para validar el proceso de la esterilización viene de, entre otras cosas, las medicinas actúa, los aparatos médicos actúan, las sustancias químicas actúan, y la ordenanza en la protección de sustancias biológicas y de la ingeniería genética. Estas leyes y regulaciones refieren a veces a directorios, a actos, o a las decisiones de la comisión, de las instrucciones, y de los estándares. Con referencia reglamentos de la UE jurídicamente vinculantes a los estándares legalmente no-obligatorios o instrucciones tales como las instrucciones del EU-GxP para
Buena práctica de fabricación (GMP)
Buena práctica clínica (GCP)
Buena práctica de laboratorio (GLP)
se dan a ley-como carácter y su conformidad es comprobada y controlada periódicamente por las agencias de estatal. El objetivo es asegurar y garantiza una norma de calidad alta y sobre todo uniforme. Cómo las regulaciones individuales se distinguen de uno a se muestra en el cuadro 1.
Según las instrucciones del EU-GxP, los sistemas y los procesos que están implicados directamente en el proceso de fabricación para los grupos de productos tales como productos farmacéuticos, ingredientes activos, cosméticos, pienso del comida, y aparatos médicos y así tienen una influencia en calidad del producto deben ser calificados y ser validados. Los requisitos de la guía a la buena práctica de laboratorio se dirigen en los laboratorios que conducen estudios no-clínicos en objetos de prueba tales como productos farmacéuticos, pesticidas, biocidas, cosméticos, productos medicinales veterinarios, aditivos alimenticios, añadidos de la alimentación, y sustancias químicas industriales. Los sistemas y los procesos usados para desactivar los materiales humanos de la muestra (fluídos corporales, tejidos, cultivos celulares, etc.), microorganismos, cultivos celulares, endoparasites – incluyendo sus formas genético modificadas – también caen bajo esta categoría.
Un requisito de los principios de buena práctica de laboratorio es que el equipo, incluyendo los sistemas automatizados validados usados para recoger, registrar, y reproducir datos y controlar las condiciones ambientales relevantes a la prueba, debe estar de diseño y de funcionamiento adecuados. Si su autoclave está implicada directamente en estudios en los grupos de productos antedichos, su conveniencia en términos de diseño y funcionamiento debe ser probada. Detalladamente, las autoridades de supervisión definirán los requisitos para la calificación y la puesta en práctica y la documentación de la validación más detalladamente especificando estándares, instrucciones, el etc. o los pueden seguir estándares porque la normalización también se mueve dentro de ciertos límites.
Calificación y validación
Como operador de la autoclave implicado en su proceso de fabricación – o como operador del laboratorio – usted es responsable de su proceso de fabricación o de los resultados y de las conclusiones de su estudio. La calificación y la validación se realiza a menudo con la ayuda de un proveedor de servicios apropiadamente calificado. Puesto que sólo usted puede definir los requisitos producto-específicos para su proceso, la colaboración estrecha entre sus departamentos del especialista, el calificador/Validator, y el fabricante de la autoclave es necesaria.
Aunque la calificación y la validación de los términos se mencionen en una frase o aún se utilicen generalmente sinónimo, las diversos declaraciones y acercamientos se ocultan detrás de ellas. El denominador común de ambos conceptos es que los documentos conforme a las instrucciones, que contienen la definición de las pruebas individuales y la documentación de los resultados de la prueba, deben ser elaborados. En muchos casos, la calificación/el plan escritos de la validación también incluye los protocolos que se utilizan para documentar los resultados de la prueba durante la puesta en práctica.
Calificación: En el contexto de una calificación del sistema, la prueba debe ser a condición de que un sistema con la tecnología usada es conveniente para la tarea prevista, trabaja perfectamente, y entrega los resultados que cumplen los requisitos. El foco principal aquí está por lo tanto en el sistema (la autoclave) y su función correcta.
Validación: El objetivo de la validación de proceso es probar que el proceso es eficaz y puede entregar un producto (resultado) que sea reproductivo y cumpla los requisitos requeridos de calidad. El foco principal está por lo tanto en el proceso sí mismo y la prueba de la conformidad con los criterios de aceptación que debe ser definida por el operador de sistema.
La calificación de proceso es a menudo un proceso que ocurre dentro de un sistema, que explica el lazo de términos. El proceso de la calificación y de validación se ilustra en el cuadro 2.
DQ – Calificación del diseño
La primera etapa de la calificación de una autoclave comienza tan pronto como usted formule y documente sus requisitos para que el dispositivo sea comprado. Esto significa que usted ha creado ya su especificación de la exigencia del consumidor (URS); es decir los requisitos que se hacen de un dispositivo y que deben ser satisfechos. Para muchos fabricantes, las autoclaves se pueden equipar de las opciones que influencian exactitud o velocidad de proceso, por ejemplo. Si ciertas opciones dependiendo de los procesos que se realizarán no se tienen en cuenta en el URS, y si no se actualizan según el dispositivo, ésta puede hacer la calificación acertada y la validación considerablemente más difíciles o aún totalmente imposibles después. Incluso en este primero tiempo, los operadores futuros deben por lo tanto especificar exactamente cuáles debe la autoclave ser utilizada para, qué requisitos deben ser colocados en los procesos, y que los estándares y las instrucciones deben ser observados.
Dependiendo de la complejidad del sistema o de la autoclave, el alcance del URS variará grandemente. Los proveedores de la autoclave presentarán una oferta sobre esta base y, en la coordinación entre el operador y el fabricante, las especificaciones serán elaboradas. La comprobación para saber si hay conformidad es un componente elemental del primer nivel de la calificación – la calificación del diseño (DQ). Después de un DQ acertado, el dispositivo es fabricado por el fabricante según las especificaciones acordadas. Al mismo tiempo (internamente, con el fabricante, o con un proveedor de servicios separado), elaborando los documentos requeridos para el índice de inteligencia subsiguiente de los pasos, OQ, y PQ (plan de la validación) pueden ahora ser comenzados. Estos documentos forman la base para ejecutar el índice de inteligencia, OQ, y PQ y especifican las inspecciones y las pruebas que se realizarán así como sus parámetros y criterios de aceptación. La documentación detallada se requiere para probar que todos los controles y pruebas se hayan terminado con éxito.
Índice de inteligencia – Calificación de la instalación
Después de que la calificación del diseño se haya terminado con éxito y el dispositivo se ha entregado con éxito, la etapa siguiente de la calificación de la autoclave puede comenzar por el sitio – la calificación de la instalación (índice de inteligencia). La conveniencia del sitio de la instalación, las características físicas de la autoclave suministrada, así como lo completo de la documentación que pertenece al dispositivo ahora se comprueban y se documentan en los documentos de la calificación. La documentación incluye generalmente las instrucciones de funcionamiento, el mantenimiento, la limpieza, y las instrucciones de la calibración así como las hojas materiales de los certificados y de datos para los componentes instalados individuales.
Si este nivel de la calificación también se ha terminado con éxito, o si algunas desviaciones que pudieron haber sido detectadas se han evaluado en base de un análisis de riesgo y de medidas apropiadas se han iniciado para eliminarlas, la calificación funcional (OQ) del sistema puede ser comenzada.
OQ – Calificación operativa
La prueba ahora está a condición de que los dispositivos, las instalaciones, las utilidades, y los sistemas resuelven los requisitos y las especificaciones del operador, que fueron especificadas dentro del ámbito de la calificación del diseño. Las pruebas se realizan para probar que el dispositivo está funcionando según plan. Esto incluye la calibración así como simula la falta, interferencia, y las condiciones del cierre del dispositivo. Este procedimiento sirve como prueba documentada que los defectos que pueden ser seguridad-relevantes o calidad-influenciando para el producto sean detectados correctamente por la autoclave.
La ejecución de los funcionamientos de la esterilización de la autoclave sin el producto introducido es también parte del alcance de la calificación funcional. Los sensores de temperatura y un sensor de la presión se insertan en la autoclave para esto, que utilizan un maderero de datos para medir la presión y la temperatura independientemente del regulador de la autoclave. Los valores de la temperatura y de la presión determinados de esta manera se pueden comprobar así contra los valores determinados vía el control de la autoclave. Además, los bioindicadores basados en bacilo stearotermofilus se introducen en las autoclaves para probar la eficacia biológica del proceso de la esterilización. El objetivo es proporcionar la prueba documentada que un sistema o un dispositivo es conveniente para su uso previsto sin un producto.
PQ- calificación del funcionamiento
Una vez que la autoclave se ha demostrado funcionar sin un producto, el funcionamiento del dispositivo se comprueba según las especificaciones del plan de la validación definió por adelantado, con el objetivo de probar que los requisitos especificados del proceso están cumplidos adecuadamente bajo condiciones reales (con un producto). Debe ser observado que la distribución de la temperatura depende del producto que se esterilizará y por lo tanto una prueba separada de PQ se debe realizar para cada configuración cargada. Los modelos de cargamento se definen para el que deba ser representante de las cargas que se esperarán en la operación diaria. Esto se hace a menudo según el esquema siguiente:
Cargamento mínimo,
Cargamento medio,
Carga del peor caso.
El peor caso que carga absolutamente se debe comprobar con respecto a la cantidad cargada, por ejemplo. Otros parámetros pueden necesitar ser considerado si podrían influenciar el resultado del proceso de la esterilización.
Como con el OQ, el proceso de la esterilización es comprobado por los sensores de la temperatura y de la presión que registran los datos correspondientes independientemente del control de la autoclave mediante un maderero de datos. Además, la eficacia biológica del proceso de la esterilización también es demostrada por los indicadores de la referencia basados en el bacilo sterothermophilus. En el PQ, a diferencia en del OQ, los sensores de temperatura así como los bioindicadores se colocan en el producto que se probará (modelo de carga) para proporcionar la prueba de la eficacia de esterilización en el producto. Es importante que los sensores de temperatura así como los bioindicadores están colocados en los puntos del producto donde se espera que un efecto de esterilización sea el más difícil de alcanzar. El objetivo es prueba documentada que un proceso puede reproductivo entregar el resultado previsto que toma en cuenta el producto.
Al realizar el OQ y el PQ, el número de puntos de la medida de la temperatura dentro de la cámara de trabajo debe cumplir con las recomendaciones de los estándares relevantes tales como EN 556 o las instrucciones de GxP, pues cualquier desviación de éstos llevará probablemente a las preguntas durante una inspección. 12 puntos de medición de la temperatura se deben por lo tanto proporcionar por 1 m3 de la cámara de la esterilización. Un bioindicador basado en el bacilo stearotermofilus se coloca en cada punto de medición de la temperatura.
Nivel de la garantía de la esterilidad
El estándar del EN 556 también proporciona la información en cuando un producto se puede describir como estéril o cuando un proceso de la esterilización se considera reproductivo, es decir entrega siempre el mismo resultado (un producto estéril). Se llama qué el nivel de la garantía de la esterilidad (SAL) se define aquí. La SAL asume una población teórica de 100 000 (105) microorganismos (unidades de la formación de colonias – CFU), por ejemplo.
El bacilo stearotermofilus se utiliza como indicador de la referencia (bioindicador) para los procesos de prueba de la esterilización del vapor. La SAL ahora exige que, dependiendo del producto que se esterilizará, la probabilidad posible más grande deba ser alcanzada que todos los microorganismos serán matados realmente y todos los productos son así realmente estéril. Esta probabilidad posible más grande se considera probada si un valor de la SAL de 10-6 se alcanza. Esto significa que la probabilidad que un producto es todavía no estéril después de que el proceso de la esterilización sea 1: 1 000 000.
Re-validación
Si todos los pasos de la calificación y las validaciones de proceso se han terminado con éxito, el operador debe especificar un intervalo para la re-validación. Es una buena idea coordinar con el fabricante de la autoclave a este punto, pues tiene sentido de combinar la re-validación con la calibración que se repite necesaria de los sensores del instrumento.
Se requiere la precaución al cambiar parámetros de proceso. Esto incluye, por ejemplo
Parámetros cambiantes del dispositivo (e.g temperatura y/o tiempo cambiantes de la esterilización);
Cambios en la configuración cargada o cambios en la composición del producto que se esterilizará,
Cambios en el empaquetado para las mercancías embaladas,
Reparaciones al equipo y al reemplazo asociado de componentes,
Actualizaciones de software del dispositivo.
Si ocurren los cambios antedichos, su influencia en el proceso total validado debe ser examinada. Si se va a ser esperado que el cambio podría tener una influencia en el proceso total, la influencia se debe determinar, evaluar, y documentar como parte de la re-validación. Esto puede dar lugar a ajustes necesarios al proceso total de modo que pueda continuar cumpliendo con los parámetros definidos antes del cambio.
Puesto que los cambios pueden también ocurrir gradualmente, es decir apenas o aún en absoluto perceptiblemente, la re-validación se debe realizar siempre en los intervalos fijos. Un intervalo de un año se ha probado aquí. Para los procesos particularmente críticos, sin embargo, el intervalo para la re-validación se puede también definir en intervalos más cortos.